Researchers at Duke Kunshan University have developed a new method for converting greenhouse gas emissions into a useful gas that offers hope in meeting the world’s clean energy needs and protecting the environment.
Dr. Kwang Leong Choy, professor of materials science at Duke Kunshan, and her co-researchers have found a way to make dry reforming of methane (DRM) technology even more effective at converting two primary greenhouse gases responsible for global warming into syngas.
The established DRM process converts methane and carbon dioxide into a mixture of hydrogen and carbon monoxide known as syngas, which serves as a key building-block intermediate and is used in the manufacturing process for industrial products such as fuel and chemicals.
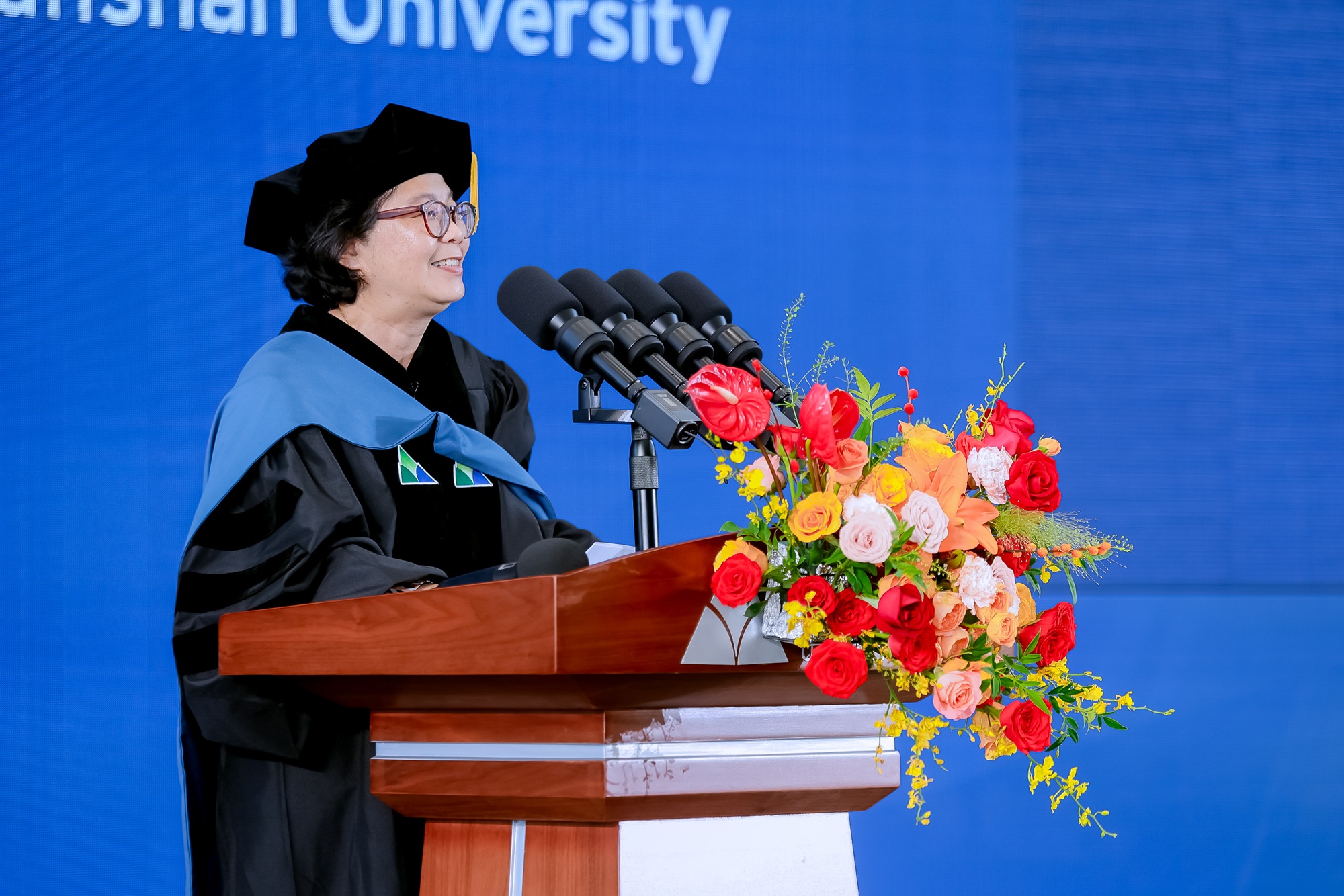
The development of the catalysts, outlined in a paper published in the journal Applied Catalysis B: Environment and Energy (impact factor: 22.1) with DKU research scientist Dr. Zi-Yian Lim as first author, has the potential to drastically reduce the carbon footprint of chemical plants without cutting production levels.
Choy said the study – “Unlocking exceptional diffusion of porous Ni@SiO2 nanocapsule catalysts for enhanced dry reforming of methane” – introduced a groundbreaking approach to enhance catalytic performance, selectivity and stability during the DRM process.
The innovation overcomes the “mass transfer barrier”, which limits the establishment of industrial reactors performing DRM or direct conversion to fuels.
“Our promising research outputs have paved the way forward for the development of catalysts, and exploration of various associated real-world practical applications in the future,” said Choy, who is acting co-director of the Environmental Research Center at DKU.
“We have successfully demonstrated the efficacy of our developed catalyst in syngas production through DRM technology.”
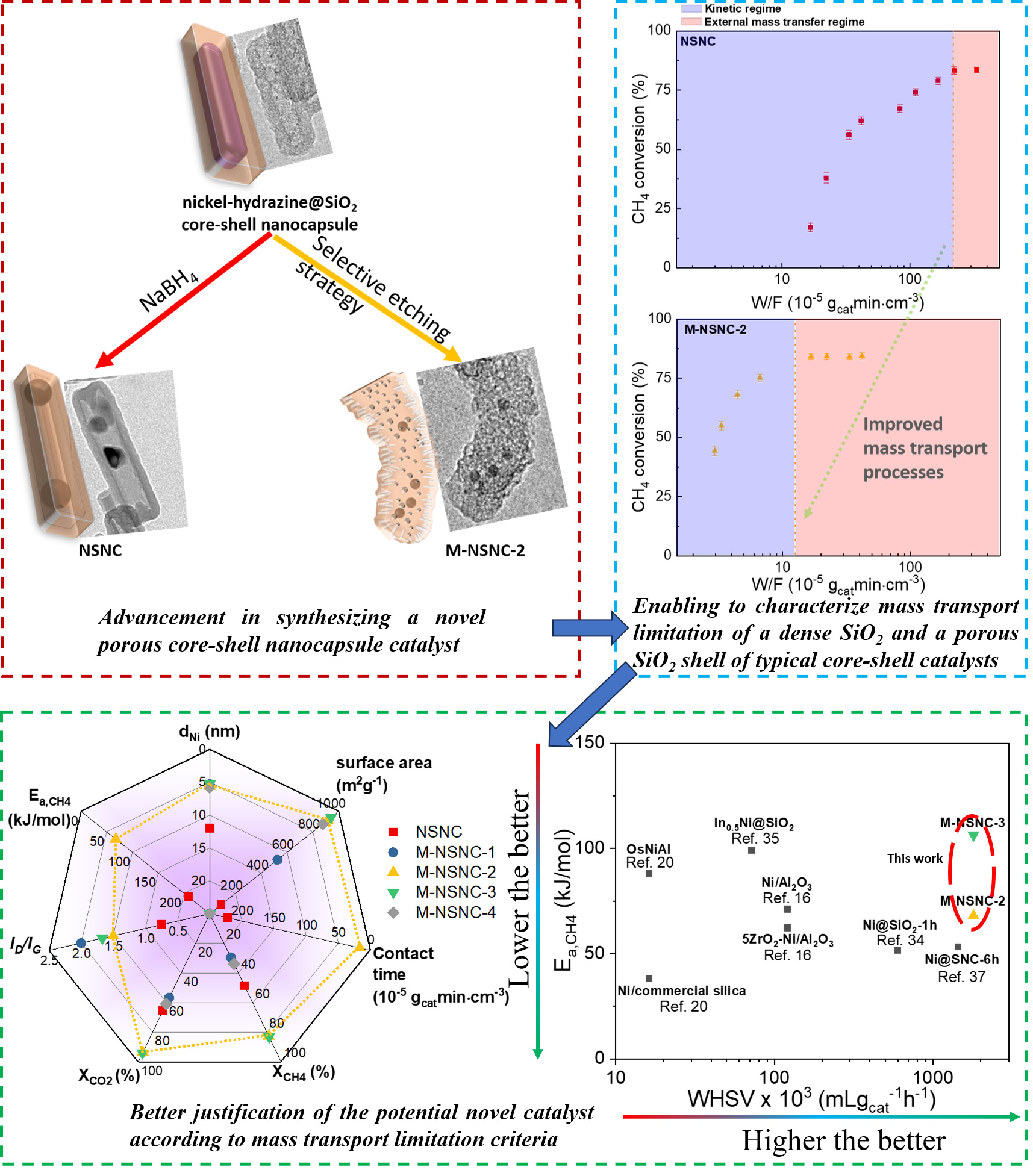
Choy pointed to the George Olah Renewable Methanol Plant in Iceland, the world’s first commercial carbon dioxide to methanol plant, as a potential beneficiary of the study.
“Overcoming the mass transfer barrier, our developed catalyst has the potential to reduce the size of the plant by a factor of 10 or increase its production by 10 times due to enhanced diffusion capabilities,” said Choy, who is the paper’s corresponding author.
“This advancement suggests that the reactor column could be smaller, economical, and safer to operate while maintaining the same production rate as a conventional reactor column.”
Alongside Lim and Choy on the research team were co-authors Junling Tu, Fengling Zhou and Baiman Chen from the Guangdong Provincial Key Laboratory of Distributed Energy Systems.
Lim and Choy developed the catalysts for laboratory-scale investigations and are now ready to expand the project for commercial use.
You can read the full paper including the author contribution statement here.